標準搭載されているシステムをフル活用
自社標準から業界標準へ─世界を広げる意識改革
未来に向かって大事な礎となるシステムの愛称は
「MIRAI」
◆生産管理システム「R-PiCS」導入事例
株式会社シバソク
従業員数:101~200名/業種:電気機械器具/導入製品:R-PiCS V4
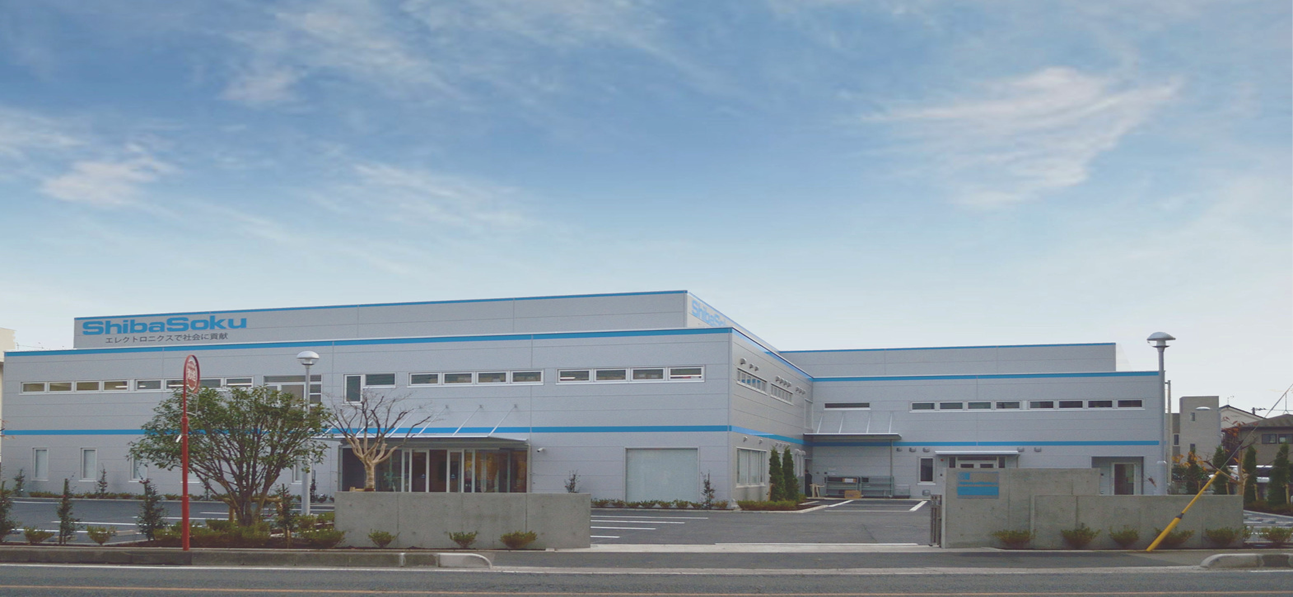
【お知らせ】2025/04/01より、JBアドバンスト・テクノロジー株式会社はJBCC株式会社と合併いたしました。
生産管理部 シニアスペシャリスト 正髙 広志 氏
総務部 情報処理課 二瓶 将人 氏
総務部 桜井 茂 氏
生産管理本部 本部長 伊藤 幹男 氏
会社プロフィール
会社名 | 株式会社シバソク |
---|---|
所在地 |
〒105-0004 |
設立 | 1955年9月7日 |
資本金 | 1億円 |
従業員数 | 139名 |
事業内容 | 半導体製造装置関連の製造・販売・修理 |
URL | http://www.shibasoku.co.jp/ |
主力製品は、半導体の良品・不良品を識別し、その品質を守るために使用される検査装置。日常にあふれるスマートフォンをはじめ、エアコンや冷蔵庫、自動車など、身近でなじみのある製品が作られる過程において、半導体テストシステムが数多く活躍している。
今回、JBATが届ける生産管理システム「R-PiCS V4」について、シバソク様の生産管理部の視点から、システム導入におけるきっかけや課題、成果など、さまざまなお話を伺った。導入の旗振り役を任された生産管理本部の本部長 伊藤幹男氏と、同じく生産管理部のシニアスペシャリスト 正髙広志氏にお話を伺った。
導入前の課題
● カスタマイズを積み重ねたことによる旧システムの複雑化
● ごく限られた人しか理解できない属人化したシステム
● 社外では通用しない「独自標準」のシステム
導入後の効果
● R-PiCS により標準搭載されたシステムを業界標準として運用し業務 スピードを向上
● 原価計算にかかる時間が4分の1へ大幅に削減
● 業者への発注業務が郵送から9 割がメール通知へ
配送費と人件費が削減
■採用の経緯について
― 新たな生産管理システムを検討するきっかけ
シバソクは1955年の創業以来、オーディオ計測器を出発点に、アナログスキルをコアとした測定技術と積み重ねた品質で、半導体の検査装置を軸に、お客様のご要望に応えた製品を提供してきた。中でも半導体は成長著しく、スマートフォンやPC、家電、自動車、医療機器、データセンター、IoT(モノのインターネット)、AI(人工知能)とあらゆる分野で利用され、今や生活に欠かすことのできない存在となっている。シバソクは、多種多様な半導体の検査装置を取り揃え、高精度かつ高品質に測定するソリューションデバイスを通して、日本のものづくりを支えている。
シバソクが大切にしているのは、『品質重視の顧客満足度』、『納品のスピード感』。 効率的な生産管理を実現させるために、生産管理システムを営業部・生産管理部・資材管理部・情報処理部と、各現場に導入してきており、「R-PiCS」は、生産管理システムとしては3代目になる。以前の旧システムは10年以上も使用されていく中で問題が生じている。それは、担当者が10年以上カスタマイズを続けた結果、限定された人しか理解できない複雑なシステムになってしまった。そうした中で、当時は5%から8%への消費増税問題もあったので、このままの継続運用はできないと判断し、新しい生産管理システムへの入れ替え検討を行うことになった。
■採用のポイントについて
― R-PiCSを採用する決め手
シバソクとJBATとのお付き合いは8年ぐらいになる。「当初、電話アポイントでR-PiCSを紹介してくれたと記憶される。ただ当時は生産管理システムの検討はしておらず、その前に会計システムを何とかしたいと相談したところ、快く会計システムメーカーを紹介してくれました。その時からのお付き合いです」。
生産管理システムの入れ替え検討の際、JBATだけでなく、複数社を交えてのコンペを行い、JBATともう1社の2社に絞り込んだ。その後、各部署にヒアリングを行い、それぞれの要望をまとめたチェックシートを使用するという、かなり慎重な選定プロセスを踏んだ。
最後は各部署のメンバーから事務局まで集めて、JBATには最終のプレゼンテーションに臨んでもらい、自分たちの仕事に一番マッチしているものは「どれか」、「費用面はどうか」、「導入期間はどれぐらいかかるのか」、さまざまな要素を比較し、社員で意見を出し合い、投票のような形でR-PiCSの採用を決定した。
■導入のプロセスについて
― R-PiCSを導入にあたっての課題
新システム導入では標準搭載されているものを使って生産管理システムを構築するというのが、社内の共通認識だった。 ところが、いざ導入が始まると「これはできないのか?」、「今まではできていたのに...」など各部署から意見が多数出てきた。これまでそういう要望を聞いては、カスタマイズを繰り返し、その結果、誰も使えないシステムになったわけだから、まずその意識を変えなくてはいけなかった。
問題になったのは『シバソク標準』という考え方。これまでのカスタマイズは、シバソクの独自の文化を反映したもので、社会全体で通用するものではなかった。新システム導入目的の一つとして、業界で使用されている『業界標準』を取り入れ、業務効率が向上だけでなく、それぞれの視野も広がることを期待した。 「ただ旧システム使用の10年間で、シバソク標準が染み付いていたため、なかなか意識改革が進まず、経営の方からも "考える知恵を持て" と発破をかけられました。」
もう一つの問題は導入期間。JBATからは事前に、稼働まで10カ月の導入期間を通知されていたが、シバソクとしては、年度が切り替わる3月の稼働切替を計画していた。なぜなら旧システムの更新もちょうど3月に行われるため。JBATは、システム稼働までの手順を5段階のフェーズに細分化し、期限を明確にし、サポート体制を整えてくれていた。しかし、シバソク標準の意識改革に加えて、月々の営業売り上げ、さらには年度末の売り上げ確保などにより、あっという間に時間が過ぎ、気がつけば残り3カ月で運用開始という切迫した状態に陥っていた。
― 導入が前進した要因
伊藤氏自身は、シバソクの関連会社から異動され、R-PiCS導入の推進を命題の一つとして、プロジェクトに途中参加。『シバソク標準』についての知識は持っておらず、R-PiCSの導入が初めての生産管理システム導入だった。そのため「なぜできないんですか?」と聞かれても「そういうシステムだから」と、切り返すことができた。 ただ、旧システムを導入した際には担当者が手厚くサポートしてくれた経緯があり、R-PiCS導入の際も同様のサポートが期待できると思っていた。
JBATからも経験豊富なSEさんが来てくれて、要求仕様に基づき、パッケージシステムをもとにした適用分析と機能要件を定義し、運用モデルの策定から機能仕様の検討、マスタ設定基準の整備と、環境を整えてくれていた。 ただ、そこから先の最も重要となる本番マスタの登録準備からは、シバソク側の作業となった。「R-PiCSは皆さんが道具として扱うものです。サポートするので頑張りましょう」と、SEさんに言われてハッとさせられました。『業界標準』の運用をする上で避けて通れないものだと思いました。システムのプロではないので苦労しましたが、言葉の一つ一つを丁寧に教えてもらい、メンバーで協力しながらフェーズを進められた。 R-PiCS導入が成功した要因の一つは、切迫した期限があったからだ。意識改革の中で主要メンバーは「R-PiCSに向き合わなければいけない」と感じ取っていたので、ある程度準備を進めることができた。キーパーソンとなる主要メンバーが着々と準備を進める中で、他のメンバーたちにも徐々にR-PiCS導入の意義が見えてきたのではないか。
シバソクはこれまで生産管理システムを導入して20年になる会社であるため、その経験から「コレはコウすればいい」、「アレはコレを使えばできる」というふうに考え方が変わってきた。JBATからも色々と支援・教育があり、ロールプレイング等で運用テストを実施した。それを動画に残し、講習に参加できなかった人に配布したり、マニュアルを準備して配布したり、社内全体がR-PiCSの切り替えに向けて、前向きに対応していった。
最終的にはチーム総力戦だった。旧システムと新システムを並行稼働しながら運用テストを繰り返し、予定より半年遅れの10月に導入が実現した。結果論だが、もし社内から専任の人間を配置して、徹底的に取り組んだ方が、導入速度が早かったかもしれない。少しでも遅れを取り戻そうと、各部署から人数を動員したものの、個々の理解力や判断力が異なり、JBATから一斉に説明を受けたにも関わらず、結果的に入力方法の違いなどから、データをやり直す事があった。 失敗しながらもみんなで向き合ったことで、R-PiCSを深く理解したというメリットも生まれた。考えようによっては、失敗は成功への近道とも考えられる。『シバソク標準』から『業界標準』へ、その道筋が明確になった。
■導入の効果について
― R-PiCSの導入効果
劇的に変わったのは業者への注文書の業務。以前は、注文書を作成・プリントアウトし、A社、B社、C社に分けて郵送する作業を全ての案件ごとに実施していた。しかし、現在は各社へ事前にR-PiCS用のCSVファイルを取り込むソフトを渡し、シバソクから注文書フォーマットを一括送信することで、同じファイルが届く仕組みになっている。これによりコストを抑え、メール一つで完結することが出来るようになった。従来通りの郵送もあるが、ほぼ9割近くの業者各社が協力してくれている。
また、R-PiCSにおける圧倒的な変化は受注品目の検索スピードの向上だ。 旧システムに比べて検索のスピードが格段にアップした。未だ曖昧検索など、不満が残る声も上がっているが、旧システムでも検索はできたが、少々使い勝手が悪く、日常業務で使うものなので、ストレス軽減にもつながっている。
そして、JBATの保守サービスであるヘルプデスクが非常に助かっている。分からない点があればヘルプデスクに問い合わせると、JBATの専任スタッフが複数人待機しており、質問に答えてくれる。導入から5年以上が経過した今もサポートは継続しているため、これも安心材料の一つ。
他にも、各部署からはさまざまな声が上がっている。 例えば、当月内検収内容の修正および引当変更が、以前のシステムには機能がなかったため専門部署に依頼する必要があったが、R-PiCSでは検収内容の修正が可能となった。画面のカスタマイズが各々で可能になったため、使用頻度が高い項目をまとめることで、操作しやすくなった。また情報処理部門からは、原価計算の時間が大幅に削減され、旧システムの60分からR-PiCSを導入したことで15分に短縮された。システムの導入効果として具体的な数字も報告されている。
― 効率化したことによる波及効果
R-PiCSには画面から直接データをコピー&ペーストする機能があり、データを一括で取り出しての分析や修正がしやすくなった。これにより毎朝9時に、受注・売上速報が関係者全員に届くようになった。これはR-PiCSのデータをもとに、別のソフトと連動させて使用しており、ワンクリックで速報を配信することができる。毎朝しっかりと速報を意識し、それぞれの情報を共有することで、社内全体の動きや働き方に、ちょっとした変化を生んだ。
受注残のデータをR-PiCSから抽出して週に一度、生産・営業へ同じメールで送っている。受注残は管理を怠ると、取引先との間にトラブルを引き起こしかねない。情報共有により、トラブルを事前に防ぎ、仕様の確定指示などもスピーディーに出せるようになった。この取り組みは、R-PiCSに変わってから始めたもの。 日々のコツコツとしたデータの積み重ねによって、情報の共有が容易になるだけでなく、データ自体の価値もより高いものになっていると考えられる。
― R-PiCSの愛称の社内公募
シバソクでは新しいシステムが導入されるたびに、親しみを込めて愛称で呼ぶことが文化となっている。R-PiCSにおいても、各部署からさまざまな名前の提案が寄せられ、その中でシバソク内での愛称として「MIRAI(ミライ)」という名前が採用された。
この名前は退職後も嘱託として勤務している大ベテランさんの提案を採用したものだそうだ。今後、「MIRAI」は自社の未来に向かって大事な礎となるシステムとして高く評価している。
■今後の展開について
― R-PiCSの導入によって見えてきた新たな課題
当初は『業界標準』として、できるだけシステムのカスタマイズをしないで導入することを心がけていたが、実際には必要最低限で、いくつかのカスタマイズを行って稼働している。導入から5年以上が経過し、システム上の細かい課題も見えてきた。ただそれらは、カスタマイズをしないで使おうと決めたシバソク側の課題と捉えている。 「社員全員が100%満足するシステムを作るなら、結局のところカスタマイズをするしか方法がありません。個々の要望へのカスタマイズを考慮したら、時間とコストがいくらあっても、キリがありません。」 まだまだ不満が出てくる時点で、R-PiCSを使いこなせていないと考える。 R-PiCSをより良く活用するためには、試行錯誤の運用はまだまだ続きそうだ。
理想は全社員がR-PiCSを使いこなすこと。ただ世代も年齢も育ってきた環境も、全く違う人間の集まりでは、どうしても得手・不得手が出てくる。 現在、R-PiCSの使用頻度は、120人中の30人程度。使える・使えないという問題ではなく、全員がR-PiCSの存在や内容を認識しつつ、使用しない人にも適切な仕組みを取り入れている。例えば、営業マンでR-PiCSを触らない人もいるが、営業アシスタントは常に利用している状態。現在の体制では、それが一番効率のいい形だと考えている。 ある程度、会社の規模や人材に応じて、スムーズな効率化を図ることも、また一つの考え方。時代の流れや状況に応じて、考え方を柔軟にカスタマイズさせてこその『業界標準』ではないか。 と伊藤氏、正高氏両名は締めくくる。