「強み」を活かすため、世の中に無い仕組みを模索、全社で獲得した「自分たちのシステム」 ◆生産管理システム「R-PiCS」導入事例
極東高分子株式会社
従業員数:201~500名/業種:プラスチック製品製造業/導入製品:R-PiCS V3
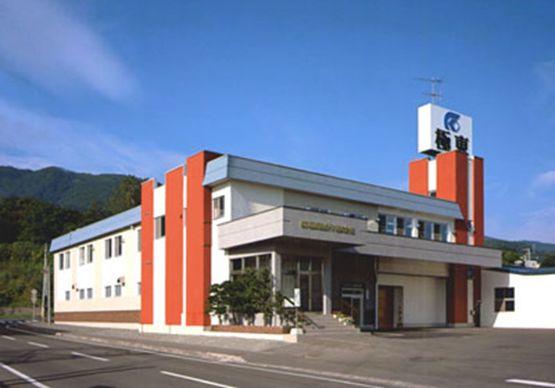
【お知らせ】2025/04/01より、JBアドバンスト・テクノロジー株式会社はJBCC株式会社と合併いたしました。
経理部 課長 広島 翔太 氏
会社プロフィール
会社名 | 極東高分子株式会社 |
---|---|
所在地 |
〒047-0261 |
設立 | 1965年9月1日 |
資本金 | 1億6,500万円 |
従業員数 | 275名 |
事業内容 | ポリエチレン製品、食品包装用を中心としたラミネート製品、成形品、段ボール製品、紙器製品の製造 |
URL | http://kyokutou-koubunshi.jp/index.shtml |
極東高分子株式会社(以下、極東高分子)は、北海道の小樽市に工場を構え、ポリエチレン製品、食品包装用を中心としたラミネート製品、成形品、段ボール製品、紙器製品の製造などを製造する「食品包装資材」の専門メーカーだ。"私たちは地球環境との調和につとめ、お客様の視点に立った品質と技術を提供し、人びととの「豊かさ」と「安全」に貢献します。"という企業理念を掲げ、それぞれの特性を生かした複合化を図れる点が最大の強みとしている。
■旧Cobolのオフコンからの脱却、キーワードは『オフコンからパソコンへ』
極東高分子の最大の特徴として、食品包装資材に関わる製造を一貫して行えるという点があり、それが同社の強みとなっている。例えば冷凍食品を入れるプラスチックのトレイや、パッケージングされているラミネート、それを出荷するための段ボールなどを一手に受注することができるメーカーは国内ではほとんど見当たらない。しかし、それぞれの製造工程が大きく異るため、生産管理のシステム化には高度でフレキシブルな要件が必要となる。
こうした背景もあり、30年くらい前から自社で開発可能なオフコンを導入し、社内のエンジニアがCobolでプログラムを書いて生産管理システムを運用している状況が続いていたという。当時の状況を振り返り、経理部 課長 広島 翔太 氏(以下 広島氏)は次のように話してくれた。
「以前のオフコン時代は、生産現場の社員からの要望があれば、それをどんどんプログラムを書いてカスタマイズしていくという状況が続いていました。
これだとやりたいようにできる反面、何かあったときのメンテナンスが大変です。
例えばプログラム1箇所直すのにも、関連する10箇所を修正しなければならないという煩雑な処理が必要で、システム部には大きな負荷がかかっていました。あとはとにかく紙が多かったですね。
旧システムでは手軽にデータの出力ができなかったので、何かを見るために使う600種類もの帳票があって、使われてないものも結構ありました」
時間が経過するにつれてCobolによるシステム改修はさらに複雑化していった。更に悪いことにはCobol技術者が高齢化していくという根本的な問題を解決するため、極東高分子では新しい生産管理システムの導入を検討することとなった。
システム導入当時にコンサル契約をしていたITコーディネーターの方から、
「これからはパッケージを使うべき」というアドバイスもあって、社内では『オフコンからパソコンへ』というキーワードで、新システムのプロジェクトを進めていったという。
<経理部 課長 広島 翔太 氏>
■9社17製品のコンペから『R-PiCS』を採用。北海道でのサポート体制もポイントに
新システム選定のため、コンサルタントのITコーディネーター主導となってベンダー調査会を行うことになったという。公募した結果、9社17製品がノミネートしてきたため、各社から新生産管理システムのプレゼンをしてもらうこととなる。
「会社の一大プロジェクトなので、実際には社員20人くらいで見て選定していきました。
その中でJBアドバンスト・テクノロジー(以下JBAT)の『R-PiCS(アールピックス、以下R-PiCS)』は、製造業に特化したパッケージであって、中小企業向けの生産管理システムとして高いシェアもあり、プレゼンも明確でわかりやすかったですね。
具体的には構成マスタ、レシピ表があれば今の業務でも便利に使えるという提案もあって、これなら自社でも使えそうなイメージが持てました。
最終的にはほぼすべての大手メジャー製品なども聞きましたが、操作性が悪そうだったり、見るからに業務と合わなかったりというのもありました。
JBATで唯一引っかかったのは北海道でのサポート体制でしたが、グループ会社が札幌に拠点があって、ハードメーカーの保守は札幌でもできることがわかったので、問題を払拭することができました」
<極東高分子の建物配置図 広い敷地に現在はポリエチレン、ラミネート、成形品、段ボール、紙器の5事業の工場と倉庫がある>
■4つの事業で4つのシステム、困難だった導入プロジェクトは「自分たちで良いものを作る」というマインドで稼働へ
システム選定を経て、極東子分子ではR-PiCSで新システムの導入プロジェクトをスタートさせる。
当時4つの異なる事業でシステムを導入する一大プロジェクトだったため、まず比較的工程が複雑でない段ボール事業から導入作業を始めることとなった。
しかし、4つの事業で新システムを導入するのは容易ではなかったという。広島氏は導入当時の状況を次のように振り返る。
「最初のプロジェクトは2010年の1月にキックオフを行って、10月から適応分析を開始。年内には適応分析を完了、というスケジュール感で進めていきました。
実際に11月にテストプログラムが出来たのですが、残念ながら思ったものにはなりませんでした。
その理由は当初のプロジェクトではあるべきシステム像をゼロベースで検討してしまったので、要件と期待が大きくなりすぎたという事情もあったと思います。
また、お互いに口頭ベースで進めていて曖昧な部分もあったので、両社合意の上で一度きちんとプロジェクトを見直そう、という決断をすることになりました」
こうして極東子分子では見直しプロジェクトとして再スタートを実施することになった。
特に難しかったのは、外部仕様書から実際に動くもののイメージを掴むのが大変だったという。
最終的に4つの事業の4つのシステムの仕様の決定と、プログラムの評価をするのに年単位の時間が必要になった。
それでもプロジェクトメンバー全員が前向きに取り組むことができたのは、「自分たちのシステムを自らの手で作っている」という実感が持てたからだと広島氏は語る。
「現場の担当に新しいシステムの動くイメージを説明するのが一番大変でした。
当社は4つの事業があり、4つの異なるシステムが動いているようなものなので、外部仕様書のチェックとプログラムの検証もそれぞれ異なる難しさがありました。
それでもJBATさんと一丸となってプロジェクトを進めていった結果、今までシステム外でやっていた原材料手配をアドオンでシステム化するなど、時間をかけてじっくりやっただけ、手の行き届いたシステムにすることができました。『お互いに良いものを作ろう』というマインドが一致していたのが成功の要因だったと思います」
2014年9月に一通りのプログラムが揃って動かせる目処がたった。工程が複雑なラミネート、ポリエチレンは次ステップにまわして、まず成形と段ボール事業から並行稼動を開始させることとなった。
「実際に新システムが動き始めてからも、いくつか問題は出てきました。
ただ、出てくる課題を事前に想定して潰していくなど、プロジェクトメンバー全員がマインド的にも前向きになって取り組むことができるようになっていました。
その背景には、長い間構築に携わってきたので、早く使ってみたいという思いが強かったからだと思います。
何より『一緒に皆で作った』という雰囲気がプロジェクト全体に浸透していったのが大きかったですね」
そこには以前のシステムは電算側が勝手に作っていたという印象が現場スタッフに根強く残っていたが、今回は現場も一緒に作ることが出来たので、皆でつくったものという意識の変革があったという。
こうして新システムが順番に立ち上がっていくこととなったが、プロジェクトの中でもポリエチレンとラミネートは一番苦労したという。
「ポリエチレン、ラミネートは原材料の取り込みのプログラムが特に大変でした。
ですが要件をきちんとまとめて作り上げた結果、おそらく他社には無いシステムができたと思います。
例えば①受注生産で使う材料を登録⇒②レシピができあがる⇒③オーダー数で所要量計算⇒④発注方法も枝分かれ、その先も枝分かれという工程があるのですが、仕入元によって発注方法が様々で、パターン化も難しい。ですが新しいシステムではそれを吸収することができました。
おかげで従来のような二重入力もなくなり、紙とオフコンとExcelで運用していたものがR-PiCSだけで処理出来るようになりました。
それ以外にもポリエチレン、ラミネートは自動スケジューラを入れるのが大変でした。
スケジューラは設定が命なので、稼働させるまでJBATさんには設定値ごとにパターンを提示してもらうなど色々とシュミレーションをさせてもらいました。
最終的に段ボール以外の3製品でスケジューラを導入し、今は無いと困るくらい活用ができています。
システムを確認すれば一瞬で機械の負荷状況が見れるので、納期回答が早くなったり、機械や人の工程管理が格段に改善できました」(広島氏)
<極東高分子でのスケジューラ シュミレーションを繰り返して利用できるようになった>
■R-PiCS の導入で獲得したリアルタイム性と全社的なシステム意識の改革
足掛け4年以上の時間を費やし、極東高分子ではR-PiCSを軸にした新システムが立ち上がることとなった。その導入効果について、広島氏は次のように話してくれた。
「一番は情報のリアルタイム性が以前と全く違うことですね。
以前のシステムではバッチプログラムで処理しないと、現在の在庫や資材の状況が翌日までわからないという状況でした。
今のR-PiCSなら、パソコンからシステムを確認するだけでリアルタイムに生産の進捗状況がわかります。以前から大幅に改善できたと営業からも感謝されました。
その他にもバーコードリーダーの導入によって、受け入れや出荷の業務がだいぶ短くなりました。
ミスの防止だけでなく、作業時間の短縮やトレーサビリティの実現にもつながっています。
そして紙が劇的に減りました。帳票の種類だけで600種類から100種類に減ったので、枚数でいうと月に数万枚の削減効果です。
社内でも画面で見られれば良いものは画面で見れば良いというという発想に変わっていきましたね。おかげで営業から工場に確認する電話の数もめっきり減りました」
こうした製造業務の効率化に加えて、何より一番意識が変わったと思うのは、システムに対する考え方だったと広島氏は指摘する。
「作業現場もシステム構築時から関わることによって、システムのありがたみが解るようになったと思います。
現場の担当者が直接システムに触る機会が増えたので、「例えばこういう処理をすれば楽になるだろう」とか、そういう知見が社内全体に育ちました。
そのおかげでよくわからないで突拍子のないことを言う人は居なくなりましたね。リアルタイムにデータがわかることの大切さが社内全体でよくわかったきたと思います」
現在の極東高分子では、社員280名全員がR-PiCSを活用しているという。
<食品のラミネート、全国的に展開しているスーパーなどにも採用されている>
■R-PiCSは無くてはならない仕組み。今後はITを幅広く活用し、事務作業を無くしていきたい
現在の極東高分子では、R-PiCSが完全に稼働し、自動スケジューラやバーコードリーダーと合わせて無くてはならない仕組みとなっている。
EUCという視点でもR-PiCSはデータベースが公開されているため、必要なデータを抽出することができる。
社内のメンバーでもExcelやAccessを使えば改善できるので、会社全体に自分で何とかしてみようという文化が根づいてきているという。
これからのシステムについて、広島氏はさらに自動化を進めたいと展望を話してくれた。
「例えば国が進めている中小企業向けのEDIなど、そういうものをどんどん活用して、現場の自動化を実現してきたいと考えています。
将来的には人間による事務処理を極力なくしていきたいですね。得意先とデータでつながれば解決する問題もたくさんあります。ITで事務処理をなくしていきたい、と考えています」